1 Introduction
1.1 Purpose
1.1.1 The purpose of this appendix is to provide the procedure for testing the efficiency of cargo pumping systems.
1.2 Background
1.2.1 The ability of the pumping system of a tank to comply with regulation 12.1, 12.2 or 12.3 is determined by performing a test in accordance with the procedure set out in section 3 of this appendix. The quantity measured is termed the ‘‘stripping quantity’’. The stripping< quantity of each tank shall be recorded in the ship’s Manual.
1.2.2 After having determined the stripping quantity of one tank, the Administration may use the determined quantities for a similar tank, provided the Administration is satisfied that the pumping system in that tank is similar and operating properly.
2 Design criteria and performance test
2.1 The cargo pumping systems should be designed to meet the required maximum amount of residue per tank and associated piping as specified in regulation 12 of Annex II to the satisfaction of the Administration.
2.2 In accordance with regulation 12.5 the cargo pumping systems shall be tested with water to prove their performance. Such water tests shall, by measurement, show that the system meets the requirements of regulation 12. In respect of regulations 12.1 and 12.2 a tolerance of 50 litres per tank is acceptable.
3 Water performance test
3.1 Test condition
3.1.1 The ship’s trim and list shall be such as to provide favourable drainage to the suction point. During the water test the ship’s trim shall not exceed 38 by the stern, and the ship’s list shall not exceed 18.
3.1.2 The trim and list chosen for the water test shall be recorded. This shall be the minimum favourable trim and list used during the water test.
3.1.3 During the water test, means shall be provided to maintain a backpressure of not less than 100 kPa at the cargo tank’s unloading manifold (see figures 5-1 and 5-2).
3.1.4 The time taken to complete the water test shall be recorded for each tank, recognizing that this may need to be amended as a result of subsequent
tests.
3.2 Test procedure
3.2.1 Ensure that the cargo tank to be tested and its associated piping have
been cleaned and that the cargo tank is safe for entry.
3.2.2 Fill the cargo tank with water to a depth necessary to carry out normal end of unloading procedures.
3.2.3 Discharge and strip water from the cargo tank and its associated piping in accordance with the proposed procedures.
3.2.4 Collect all water remaining in the cargo tank and its associated piping into a calibrated container for measurement. Water residues shall be collected, inter alia, from the following points:
|
.1 |
the cargo tank suction and its vicinity; |
|
.2 |
any entrapped areas on the cargo tank bottom; |
|
.3 |
the low point drain of the cargo pump; and |
|
.4 |
all low point drains of piping associated with the cargo tank up to the manifold valve. |
3.2.5 The total water volumes collected above determine the stripping quantity for the cargo tank.
3.2.6 Where a group of tanks is served by a common pump or piping, the water test residues associated with the common system(s) may be apportioned equally among the tanks provided that the following operational restriction is included in the ship’s approved Manual: ‘‘For sequential unloading of tanks in this group, the pump or piping is not to be washed until all tanks in the group have been unloaded.’’
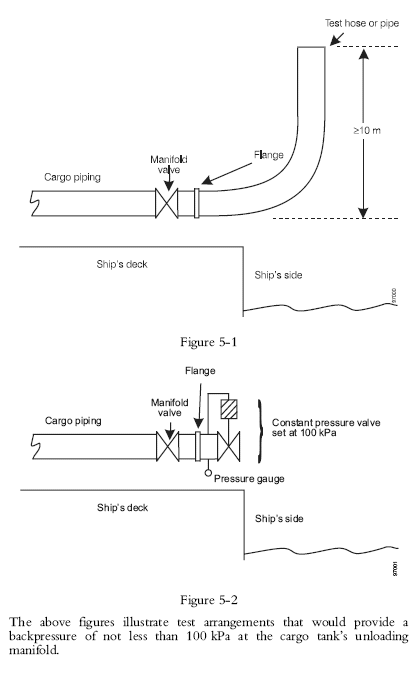
|